PRODUCTION AREA
OSMOSIS PLANT:
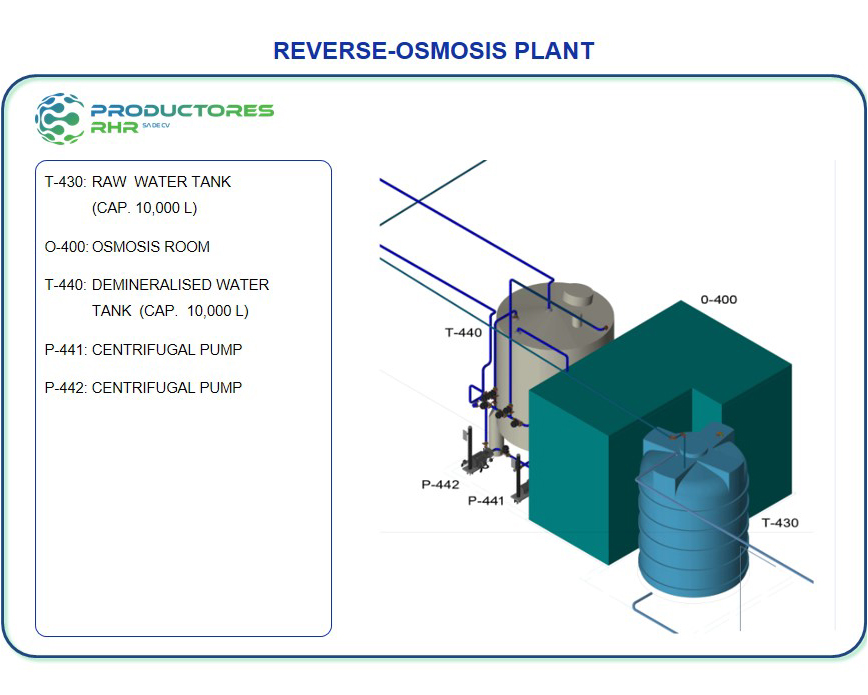
For the catering of the demand of water in the production area, we have a raw water treatment system to obtain reverse osmosis quality water adequate to use in biomass and biosynthesis production processes.

The plant is fully automated, which has raw water softening filters and demineralizers, in addition to the membrane system. The whole system is adequately connected to sanitary grade pumps, valves and piping in order to supply the water loop in bioreactor areas. It is worth mentioning that the plant counts with two tanks with a balance of 20,000 L, one polyethylene tank as raw water deposit and the second one with a 316L capacity, made up of stainless steel used as a balance tank and treated water supply.
The reverse osmosis water treatment system has a production capacity of 15 m3/h of reverse osmosis quality water.
BIOREACTORS AREA:
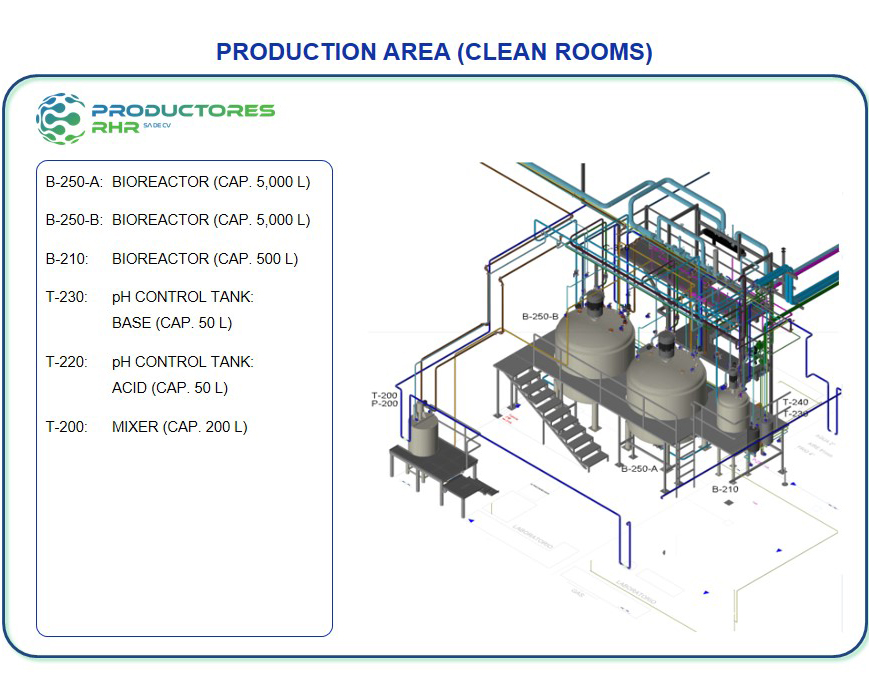
This area is distinguished by the sanitary design it was built on. It has epoxy floor and sanitary finish. This part of the complex is divided in several sections due to the own demands of the process since it is necessary the real-time monitoring of the process. It has rooms aimed to microbiologic and physiochemical control laboratories, with a section of locks for staff, an office, and a mixing room for the creation of cultivation channels. The room is equipped with a 316L stainless steel tank with agitators, with usability of up to 500L when connected directly into the tanks of work.
In regards to the main bioreactor area, we have a battery for three torispherical tanks, 316 SS, two tanks with nameplate capacity of 5,000 L and one of 500 L. The three tanks have deflectors, an agitator system that has an agitator such as Rushton’s (to support the dissemination of oxygen dissolved in the cell) and one agitator like marine propeller’s (to support the mixing of the cultivation). To ensure an efficient dissemination of oxygen to the cells, the tanks have sintered steel diffusers connected to the agitator.
The reactors’ battery is directly connected to the hygienic extraction area by pipes, valves, unions and pumps with hygienic design, in addition to have a regulated weather by means of mini-splits. It is worth pointing out that this area is prepared for the expansion of greater capacity tanks (up to 20,000L) since the foundations were reinforced.
The configuration for the distribution of services for this section has been staged in the upper part of this area: piping (gas, reverse osmosis water, sterile air, and sterile vapor, refrigerant), vapor train, air filters, and sensors controllers for the bioreactors bioreactor exhaust pipe, etcetera.

With the infrastructure of this area, it is possible to carry out escalations of We can scale up the biotechnological processes as well as the industrial production of it with the infrastructure in this area. From the efficient production of biomass (yeasts, fungi, and bacteria mainly) to the obtainment of secondary metabolites through biosynthesis. This is possible due to the effort and seriousness placed on the design of the area, as well as the piping and instrumentation of the same one. These provide the hygienic, service, and automation conditions – optimal for the development and efficient production of the biotechnology projects.
BIOREACTORS SERVICES:
The bioreactors are supplied with the necessary services for the production of biomass and biosynthesis, such as: inverse osmosis quality water, vapor and refrigerant distributed straight to the jacket; sterile air obtained by filtration; liquid reagent distribution (acids, bases, and defoamer) through peristaltic pumps. In regards to the physiochemical monitoring of the process’ parameters; the reactors are equipped with pH, dissolved oxygen and temperature sensors built into the Programmable Logic Controller, which automate the control of such conditions.
SANITARY EXTRACTION:
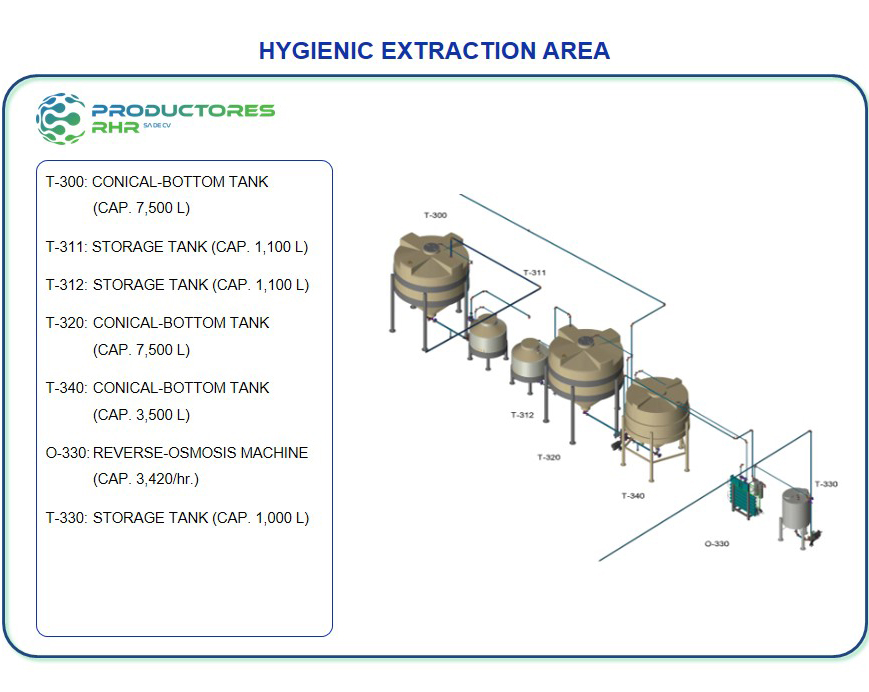
This section of the plant is also distinguished by its sanitary design since at this stage it is absolute important to keep the stability and integrity of the biomass or the secondary metabolites produced. It has epoxy flooring and sanitary finish. It is also built by a centrifuge with disk separators used in the decantation of the biomass from the liquid cultivate. It is also connected to pumps for the distribution on toppers as balance tanks to achieve processes in ¨batches¨ and get the optimal clarification for the liquid medium and greater cell recovery.
The balance tanks with the clarified medium are connected to the chemical extraction through piping and pumps with hygienic design. There’s also the option of decreasing the workflow volume by concentrating the cultivation medium by reverse osmosis membrane system, with the purpose of making the extraction more efficient.
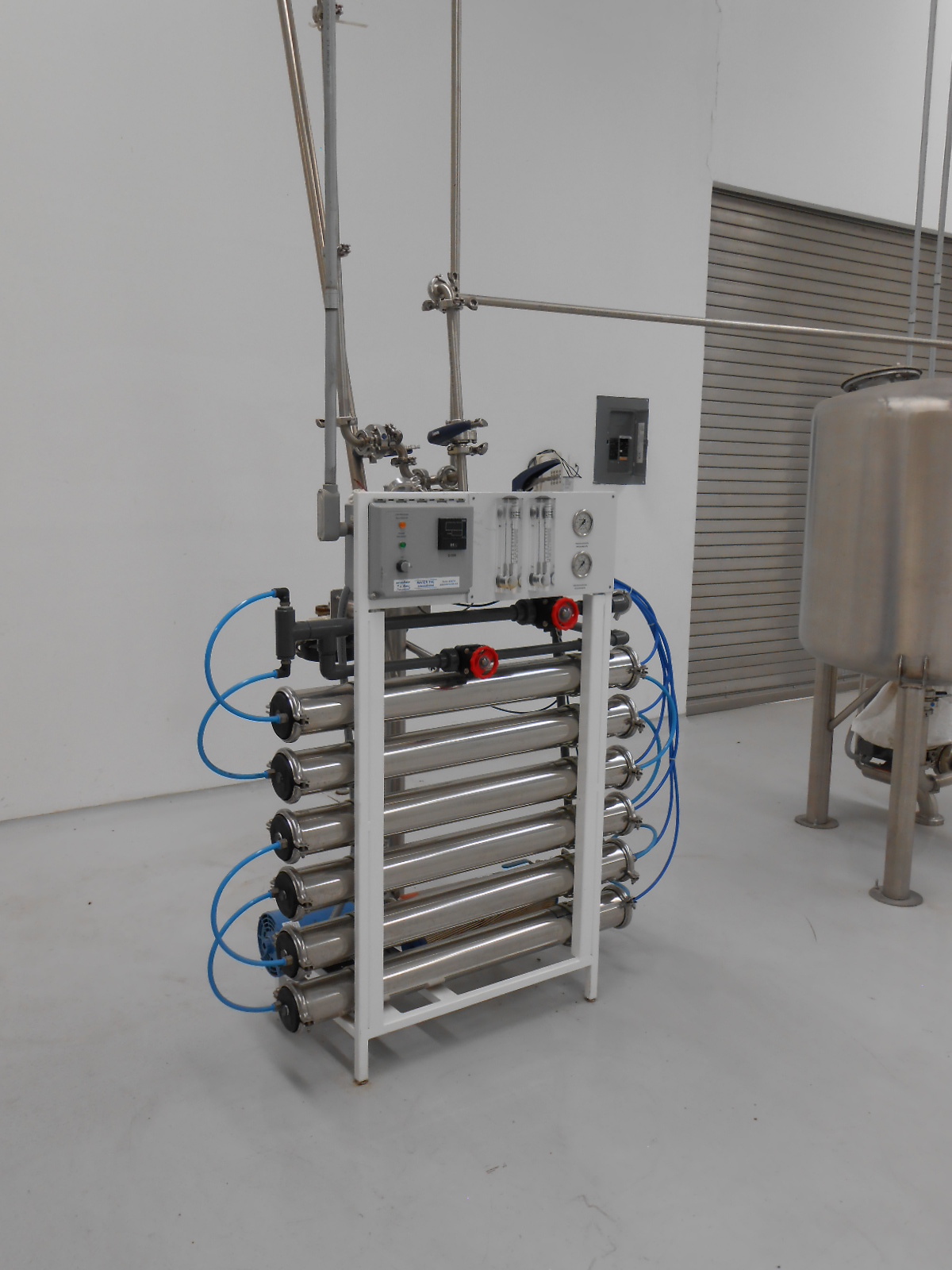
We guarantee the separation of the cells and cultivation medium for its subsequent treatment, procuring the integrity of the compounds of interest with the integration of this area.
CHEMICAL EXTRACTION:
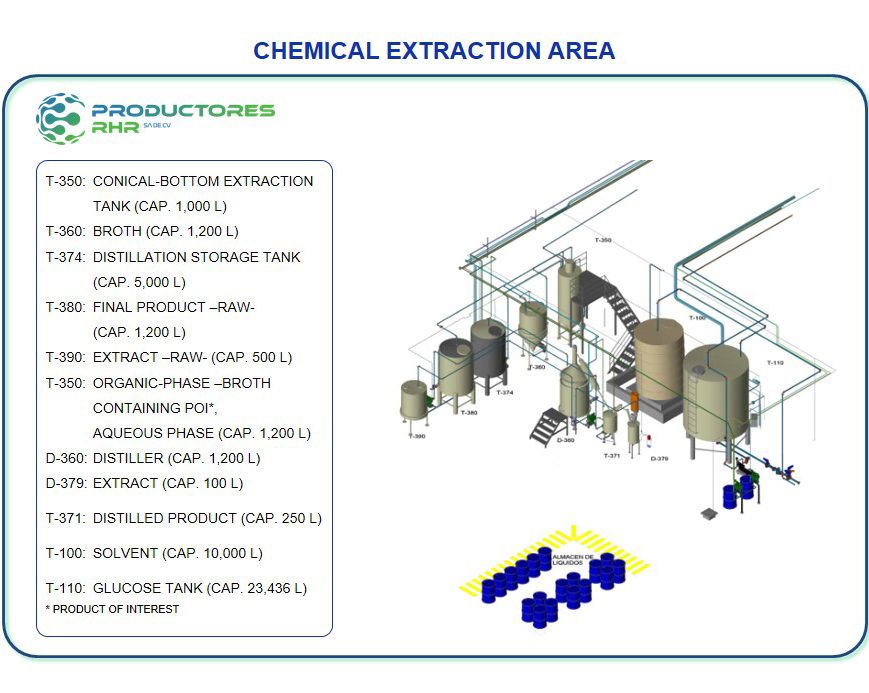
This area of the plant is separated from the clean areas and it is only connected to the pipes with the hygienic extraction area due to the hygienic conditions required for biotechnology processes. This area is built up by a very complete tank battery, since operations from extraction to distillation process are covered.

It is integrated by a stainless steel extractor tank (1,200 L capacity) with a semi-automated agitation system built into a pneumatic pump and chutes as balance tanks, mainly designed for the extraction of secondary metabolites produced through biosynthesis.
There are funnel shaped chutes for the optimal separation of phases during the extraction operation, plus there are two jacketed reactors. These are mainly employed as distillers since they were designed to be multifunctional, one has 1,200 L nominal capacity and the other one has 80 L (mainly used for the scaling of reactions). These reactors can carry out reduced pressure distillation since it is connected to a vacuum pump that provides the capacity to distil thermolabile secondary metabolites.
The tank’s heating is accomplished through isolated resistances in the reactors’ jacket and are covered with mineral oil resistant to high temperatures. In regards to the refrigerants to distillate, little tubes that distribute cool ethylene glycol to ensure the effective caloric exchange during the process are created. The reactors employed in distillation are semi-automated by a control panel for the temperature’s monitoring and agitation mainly. It is very important to mention that the pumps used in this area are pneumatic to avoid risky situations when working with flammable solvents. The equipment’s and piping connections and gaskets are made up of Teflon mainly, due to the corrosiveness of some solvents.
For the product’s storage, there’s a 2,000 L balance tank and another one from the same capacity for the distribution of solvent for the extraction and distillation operations. In this same area but an isolated one, there are two tanks, one of 10,000L and another of 25,000L in capacity. The first one is made up of high density polyethylene and it’s used for storage and distribution of chemical reagents needed for biosynthesis. It is connected to piping and pumps for distribution from the supplier to the bioreactors area. The second one is a jacketed tank and thermally isolated with the purpose of keeping the optimal temperatures for fructose syrup and/or glucose used as carbon sources for biotechnological processes. This tank is connected to piping ready for the supply of the provider and for the distribution to bioreactors in the hygienic area.
In regards to services, the area is covered by supply of water, electricity, refrigerant, vacuum and air mainly. There’s also a septic tank for the treatment of the cultivation medium’s residue.
WAREHOUSES:
The warehousing area is divided into two sections: Solids warehouse and liquids warehouse. The solids warehouse is located a few meters from the hygienic area, mainly for the fast and easy mobilization of the reagents for the preparation of cultivation mediums. Composed by two digital scales, one with a 200 Kg capacity and the second one 50 Kg, trolleys for the mobilization of sacks or kegs, pallets for the proper storage of chemical reagents and delimitation of the area by a metallic wire mesh.

The liquids warehouse is located next to the chemical extraction area, due to the demand of solvents required in this area. There are pallets for the proper storage of reagents and electrical isolation due to the nature of the reagents.
